Die Cast Mold Makers: Revolutionizing Metal Fabrication
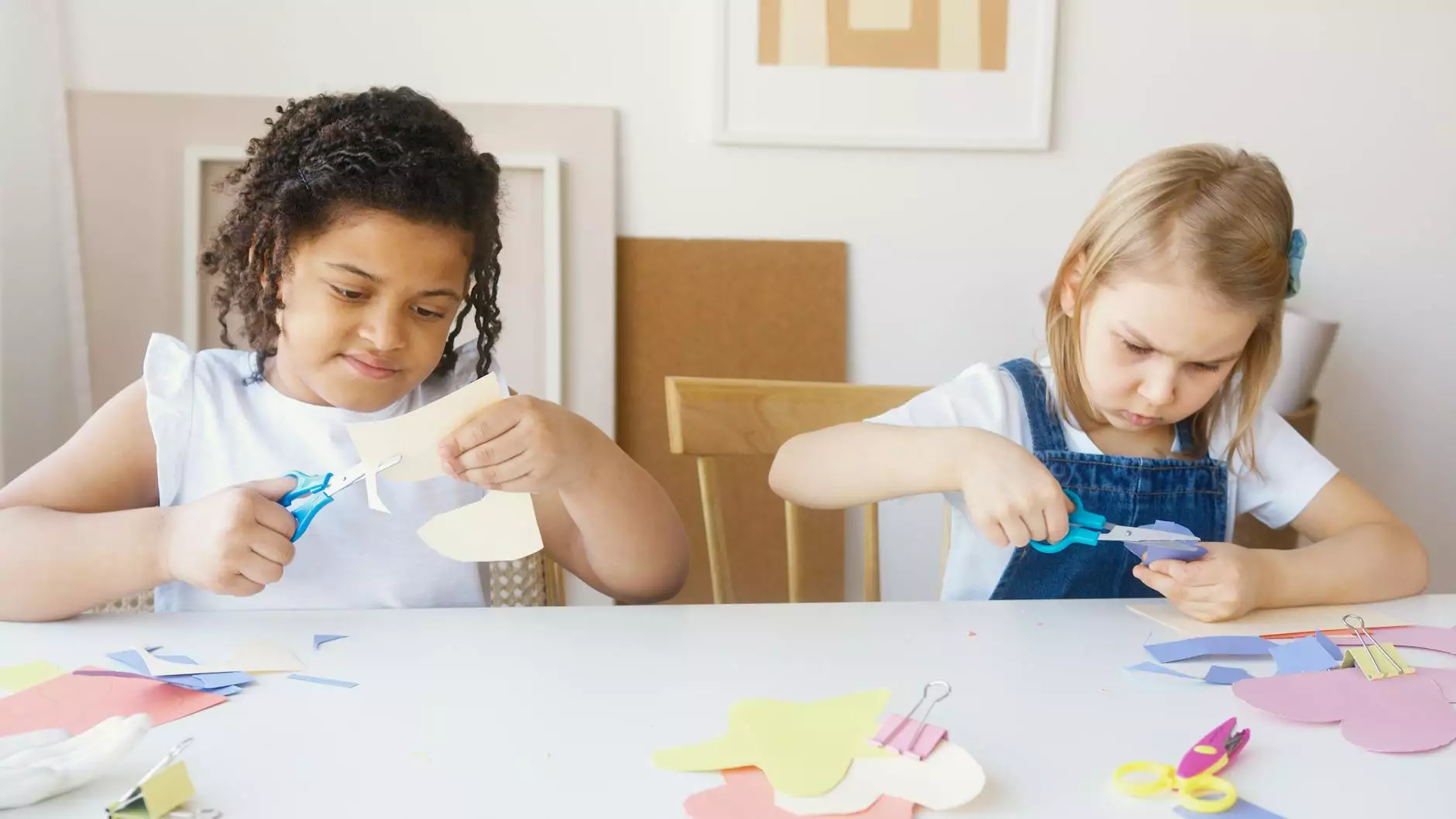
In today’s competitive manufacturing environment, die cast mold makers play a crucial role in the production process. As experts in crafting intricate molds for die casting, they enable industries to create high-quality metal components efficiently and cost-effectively. This article explores the significance of die cast mold makers, the processes they employ, and the numerous advantages they bring to the metal fabrication landscape.
The Importance of Die Cast Mold Makers
Die casting is a highly regarded manufacturing process that involves forcing molten metal into molded cavities. The precision of this technique largely depends on the quality of the molds used. Die cast mold makers are specialized artisans equipped with the knowledge and skills to design and manufacture these molds. Their expertise ensures that the final products meet stringent specifications while maintaining optimal performance.
Key Functions of Die Cast Mold Makers
- Designing Molds: Utilizing advanced software to create detailed designs that consider all production parameters.
- Material Selection: Choosing suitable materials that guarantee durability and heat resistance for the molds.
- Precision Engineering: Employing CNC machines for accurate manufacturing to achieve tight tolerances.
- Quality Control: Implementing rigorous testing to ensure molds meet intended specifications before they are used in production.
Understanding the Die Casting Process
The die casting process entails several stages, each critical to achieving the desired outcomes. Understanding these stages helps clarify why the role of die cast mold makers is indispensable.
1. Mold Design and Prototyping
The first step in die casting is mold design. Professional mold makers utilize Computer-Aided Design (CAD) software to develop mockups of the molds. This stage allows for the simulation of the die casting process, identifying potential issues before physical production begins. Prototyping is essential for testing and refining designs to ensure they function as intended.
2. Mold Fabrication
Once the designs are finalized, mold makers begin fabricating the molds. Typically made from high-quality steel or aluminum, molds are constructed using advanced machining techniques. The precision achieved during this step is pivotal—the better the mold, the higher the quality of the finished product.
3. Die Casting
With molds ready, the next phase is the die casting itself. Molten metal is injected into the mold under high pressure. The speed and accuracy of this process depend significantly on the quality of the molds provided by the die cast mold makers.
4. Finishing Work
After the metal has cooled and solidified, the molds are opened to release the cast parts. Additional finishing processes, such as trimming, drilling, or surface treatment, may be applied to enhance the quality and appearance of the final product.
Advantages of Working with Professional Die Cast Mold Makers
Choosing the right die cast mold makers can yield significant benefits for companies involved in metal fabrication. Here are some of the main advantages:
1. Enhanced Product Quality
High-quality molds result in superior parts. Professional mold makers understand how various factors, like material selection and mold design, impact the final product. Their expertise leads to higher precision and fewer defects.
2. Cost-Effectiveness
Although the initial investment in quality molds can be higher, the long-term savings are often substantial. More durable molds lead to less frequent replacements and lower production costs over time. Moreover, efficient production processes contribute to reduced labor and operational expenses.
3. Shorter Lead Times
Experienced die cast mold makers possess the skills to produce molds quickly without sacrificing quality. The time saved during the design and production phases can significantly shorten the entire manufacturing schedule, allowing companies to meet tight deadlines and respond more quickly to market demands.
4. Customization
Every industry has unique requirements. Expert mold makers can create customized solutions tailored to specific needs. This flexibility enables businesses to innovate and develop new products that stand out in the marketplace.
Choosing the Right Die Cast Mold Makers
With numerous options available, selecting the best die cast mold makers for your projects is crucial. Here are some tips to consider:
1. Experience and Expertise
Look for mold makers with a profound understanding of die casting and extensive experience in the industry. Consider their portfolio to evaluate their work quality.
2. Technology and Equipment
Modern die casting requires advanced technology. Ensure that the mold makers you choose utilize the latest machining tools and software to deliver superior results.
3. Customer Testimonials
Review feedback from previous clients to gauge the company's reliability and quality of service. Positive testimonials can provide insights into their capabilities.
4. Communication and Support
Effective communication is essential for successful projects. Choose mold makers who are responsive and willing to collaborate throughout the process.
Applications of Die Cast Mold Makers
The versatility of die casting makes it suitable for various industries. Here are some common applications where die cast mold makers are instrumental:
- Automotive Industry: Producing components such as engine blocks, housings, and brackets.
- Consumer Electronics: Manufacturing parts for gadgets like smartphones, laptops, and home appliances.
- Industrial Equipment: Making durable components for machinery and tools.
- Aerospace: Creating lightweight yet strong parts essential for aircraft performance.
The Future of Die Casting and Mold Making
As industries evolve, so too do the methods and technologies associated with die casting. The future of die cast mold makers is bright, driven by advancements in automation, artificial intelligence, and materials science. Here’s what to expect:
1. Automation and Robotics
The integration of automation in mold making and die casting processes is on the rise. Automated systems and robotics can increase production efficiency and reduce human error, leading to even greater precision and quality.
2. Advanced Materials
There’s ongoing research into new materials that can endure higher temperatures and pressures. The use of advanced alloys and composites could revolutionize mold making, facilitating the production of more complex parts.
3. Sustainability Practices
With a growing emphasis on sustainability, die cast mold makers are likely to adopt eco-friendly practices. This includes optimizing energy use in manufacturing and utilizing recyclable materials whenever possible.
Conclusion
In conclusion, die cast mold makers are vital players in the metal fabrication realm. Their expertise in mold design and production significantly influences the quality, efficiency, and cost-effectiveness of die casting processes. As the industry progresses, these professionals will continue to adapt and innovate, driving growth in various sectors. Companies that invest in high-quality mold making will undoubtedly reap the rewards of superior products and streamlined operations.
For businesses looking to enhance their metal fabrication processes, seeking reputable and experienced die cast mold makers, like those at DeepMould.net, is an essential step towards achieving excellence in production.