Understanding China Die Casting Molds: The Future of Metal Fabrication
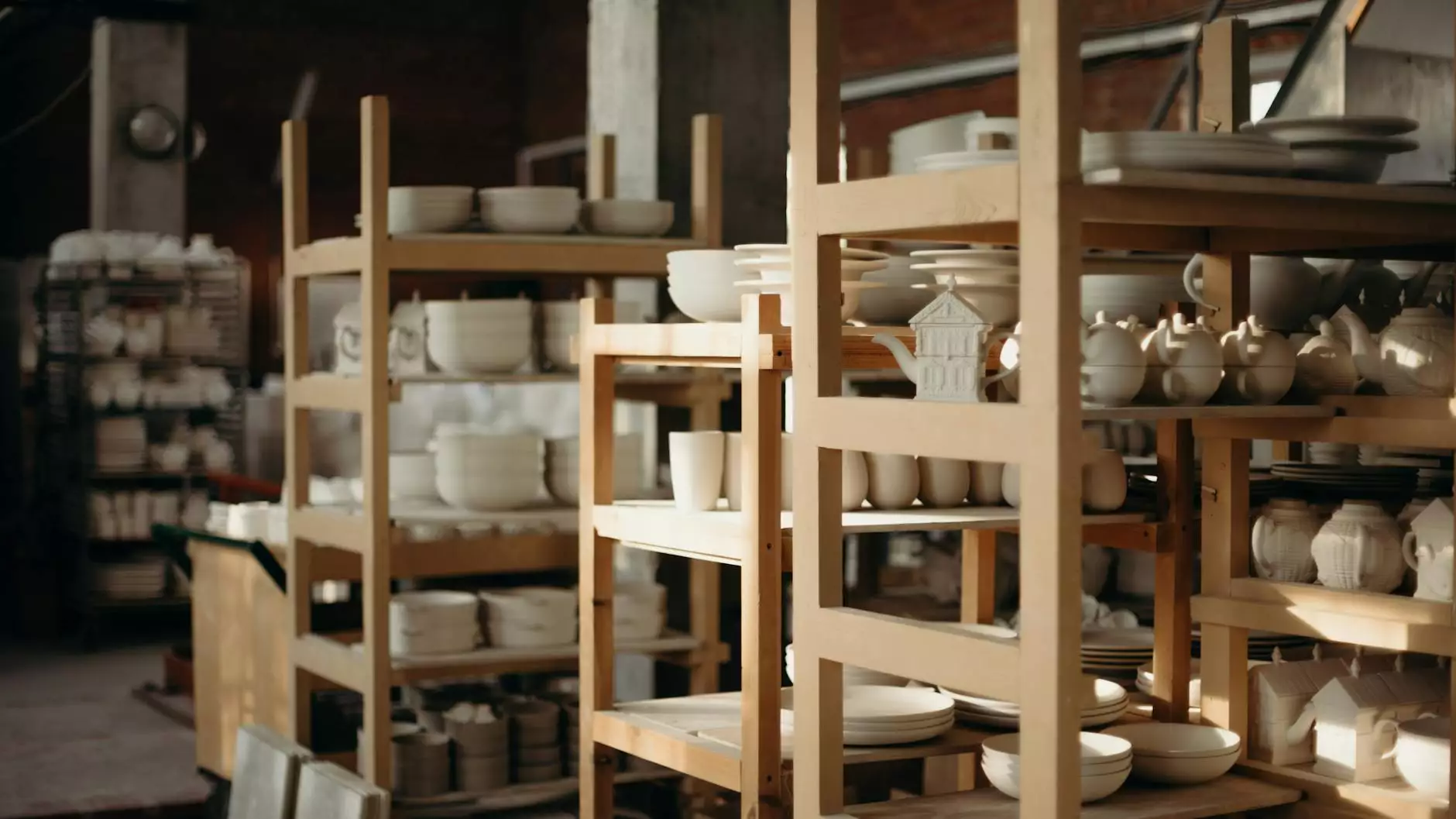
China die casting molds have revolutionized the metal fabrication industry by providing high-quality solutions that enhance manufacturing processes. In an era where efficiency and precision are paramount, understanding the benefits and applications of these molds is crucial for businesses aiming for growth and competitiveness. This article delves into the various aspects of die casting, the advantages of sourcing molds from China, and the future outlook of this dynamic field.
A Deep Dive into Die Casting
Die casting is a manufacturing process that involves forcing molten metal into a mold cavity. The process is particularly favored for producing complex shapes with high precision and excellent surface finishes. The following are key features of die casting:
- High Production Rate: Die casting can produce a large number of parts in a relatively short period.
- Dimensional Accuracy: Parts produced have tight tolerances, ensuring that components fit together perfectly.
- Surface Finish: The molds can deliver smooth finishes, reducing or even eliminating the need for additional machining.
- Material Variety: Common metals used in die casting include aluminum, zinc, magnesium, and copper alloys.
The Importance of Molds in the Die Casting Process
The mold is perhaps the most critical component in the die casting process. It determines the final shape and the dimensional accuracy of the manufactured part. Here’s why the quality of the mold matters:
- Durability: High-quality molds can withstand the intense pressure and temperatures of molten metal, resulting in longer lifespans.
- Precision Engineering: Molds designed by experienced engineers ensure that the resulting castings meet exact specifications.
- Cost Efficiency: While the upfront costs of quality molds may be higher, they lead to savings in production costs due to fewer defects and reworks.
Why Choose China for Die Casting Molds
China has become a global hub for manufacturing, and the die casting industry is no exception. Here are some compelling reasons why businesses consider sourcing China die casting molds:
1. Cost-Effectiveness
One of the most significant advantages of manufacturing in China is cost savings. Labor and material costs are generally lower, allowing for competitive pricing on molds without compromising quality.
2. Advanced Technology
Chinese manufacturers are increasingly adopting advanced technology and innovations. This commitment to modernization results in high-quality molds that meet international standards.
3. Skilled Workforce
China boasts a vast pool of skilled engineers and technicians experienced in die casting and mold making. Their expertise contributes to the production of complex and precise molds.
4. Expanding Infrastructure
The rapid industrial growth in China has led to the development of advanced facilities and infrastructure, which further enhances production capabilities and efficiency.
Types of Die Casting Molds Made in China
In China, several types of die casting molds are manufactured to cater to varying industrial needs:
1. Cold Chamber Die Casting Molds
Suitable for metals with high melting points, these molds require the metal to be heated separately before being injected into the mold. They are commonly used for aluminum die casting.
2. Hot Chamber Die Casting Molds
This type allows the molten metal to remain in the casting chamber for repeated use and is well-suited for low-melting-point metals like zinc and lead.
3. Die Casting Inserts
Inserts are components added to the mold to create specific features or details in the final product. These allow for even greater customization in the manufacturing process.
Applications of China Die Casting Molds
Die casting molds are extensively utilized across various industries due to their versatility:
- Automotive Industry: Production of engine components, frames, and other critical parts.
- Electronics: Manufacturing enclosures and structural components for devices.
- Aerospace: Critical parts that require high precision and quality standards.
- Consumer Goods: Items ranging from kitchen appliances to hardware components.
Quality Control in Die Casting Mold Production
Ensuring the highest quality standards in mold production is vital. Manufacturers often implement stringent quality control measures:
1. Material Inspection
Utilizing materials that meet international specifications is fundamental. Companies often test and verify material properties before commencing production.
2. Dimensional Tolerance Checks
Components are measured using advanced equipment to ensure they conform to the defined tolerances throughout the manufacturing process.
3. Performance Testing
Before mass production, prototype molds are tested to assess functionality and performance, identifying any potential issues that need addressing.
The Future of Die Casting and Molds Industry
As industries evolve, the die casting sector is also set to witness significant changes. Here are some trends shaping the future of China die casting molds:
1. Automation and Robotics
The integration of robotics and automation in manufacturing processes will enhance efficiency and accuracy while reducing human error.
2. Sustainable Practices
With an increasing emphasis on environmentally friendly practices, manufacturers are adopting sustainable materials and processes in their production lines.
3. Advanced Materials
As technology progresses, new materials offer greater strength-to-weight ratios, resulting in better performance in various applications.
4. Digital Manufacturing
Technologies like 3D printing and computer-aided design (CAD) are set to revolutionize mold design and manufacturing, allowing for unprecedented customization.
Choosing the Right Manufacturer for China Die Casting Molds
When selecting a partner for die casting molds, consider the following factors:
- Experience: Look for manufacturers with a proven track record in producing high-quality molds.
- Technical Expertise: Ensure the manufacturer has skilled engineers who are well-versed in the latest technologies and techniques.
- Certifications: Check for industry-standard certifications that reflect the quality management systems implemented by the manufacturer.
- Customer Reviews: Research feedback from previous clients to gauge the manufacturer’s reliability and service quality.
Conclusion
In conclusion, the significance of China die casting molds in modern manufacturing cannot be understated. They symbolize the confluence of technology, efficiency, and innovation in the metal fabrication industry. Whether you are involved in the automotive sector, electronics, aerospace, or other industries, understanding the benefits and applications of die casting molds can help streamline production processes, enhance quality, and promote cost savings.
Investing in quality die casting molds is not merely a decision; it is a strategic move that can position your business for success in today's competitive landscape. As globalization continues to influence manufacturing practices, partnering with reliable Chinese manufacturers may well be the key to unlocking new opportunities.