Exploring the World of Plastic Rapid Prototypes Manufacturers
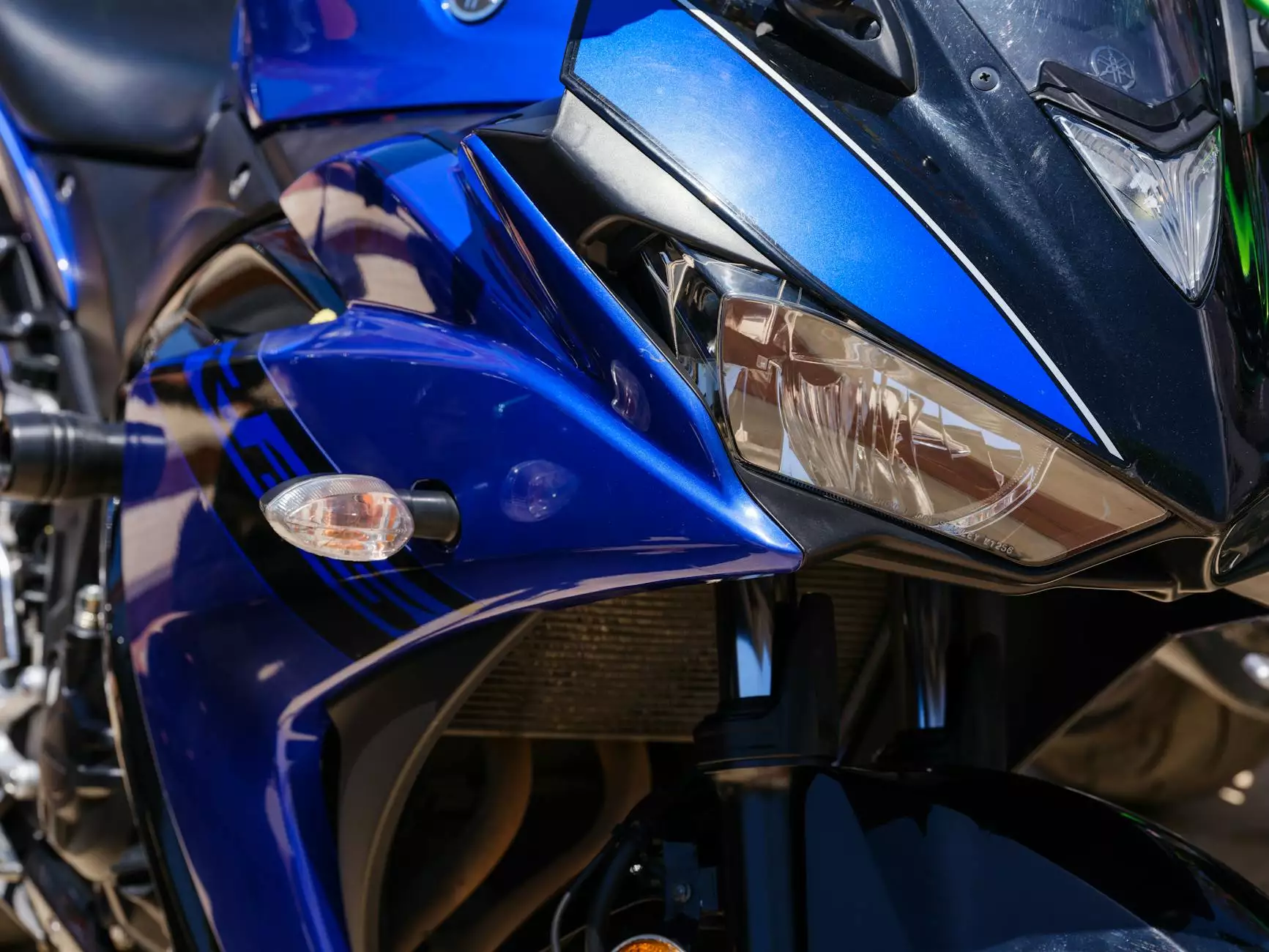
In today’s fast-paced manufacturing landscape, plastic rapid prototypes manufacturers play a crucial role in driving innovation and efficiency. These manufacturers specialize in creating realistic and functional prototypes that allow companies to refine their designs swiftly and effectively. This comprehensive article delves into the significance of rapid prototyping, the techniques employed by these manufacturers, and the overall impact on the manufacturing industry.
The Essence of Rapid Prototyping
Rapid prototyping is a revolutionary method that enables designers and engineers to create prototypes quickly for testing and evaluation. This process significantly reduces the time and cost associated with traditional manufacturing methods. The primary aim is to move from concept to product with minimal delay, allowing businesses to stay competitive and respond to market demands efficiently.
What is Rapid Prototyping?
Rapid prototyping refers to a range of techniques used to synthesize a scale model of a physical part or assembly using three-dimensional (3D) computer-aided design (CAD) data. These prototypes can be manufactured using various methods, including:
- 3D Printing - A popular technique where material is added layer by layer to build a part.
- SLA (Stereolithography) - A method that uses lasers to cure resin into solid parts.
- FDM (Fused Deposition Modeling) - A common 3D printing technology that extrudes thermoplastic filament.
- Injection Molding - A traditional method that can also support rapid prototyping through quick mold creation.
Advantages of Working with Plastic Rapid Prototypes Manufacturers
Partnering with plastic rapid prototypes manufacturers provides numerous advantages that can streamline product development processes. Here are some of the key benefits:
1. Speed to Market
The most significant advantage of utilizing rapid prototyping is the speed to market. Manufacturers can produce prototypes in days rather than months, enabling businesses to test and iterate their designs swiftly.
2. Cost Efficiency
By identifying design flaws early in the prototyping phase, companies can reduce costs associated with material waste and labor in later production stages. This cost savings is crucial for startups and established businesses alike.
3. Enhanced Design Flexibility
Rapid prototyping allows for modifications to be made with ease. Manufacturers can quickly adjust designs based on feedback, ensuring the final product meets the expectations and specifications of end-users.
4. Improved Quality
Producing prototypes enables rigorous testing and quality assurance before mass production. This reduces the risk of defects, ensuring that the final products possess the highest possible quality standards.
How Plastic Rapid Prototypes Manufacturers Operate
Understanding the operation of plastic rapid prototypes manufacturers sheds light on their capabilities and the technology they use:
1. Understanding Client Needs
The process typically begins with consultations where manufacturers assess the specific needs of their clients. This includes understanding the intended application, budget constraints, and timeline for production.
2. Design Development
Once the requirements are clear, manufacturers often help design the prototypes using advanced CAD software. This collaborative process ensures the design closely aligns with the client's vision and functional needs.
3. Material Selection
The choice of material is critical in prototyping. Manufacturers work with various plastics, ensuring they choose the best material that replicates the functional and aesthetic qualities of the final product. Common materials include:
- ABS (Acrylonitrile Butadiene Styrene)
- PLA (Polylactic Acid)
- Nylon
- TPU (Thermoplastic Polyurethane)
4. Production of Prototypes
With the design and materials finalized, manufacturers utilize their selected prototyping technologies to produce the prototypes. This stage may involve various methods based on the complexity and volume of the prototypes required.
5. Testing and Feedback
Once the prototypes are produced, they undergo rigorous testing. Feedback from these tests is invaluable, as it often leads to further refinements and optimizations. This iterative process is paramount to achieving the desired product quality.
Real-World Applications of Plastic Rapid Prototyping
The applications of rapid prototyping span numerous industries. Some notable examples include:
1. Automotive Industry
In the automotive sector, rapid prototyping allows for the swift development of components, interior designs, and functional parts, enabling manufacturers to innovate and respond to consumer demands rapidly.
2. Medical Device Manufacturing
Medical device companies utilize rapid prototyping to create functional models of devices ranging from surgical instruments to diagnostic equipment. This process accelerates the validation phases and ensures compliance with stringent regulations.
3. Consumer Electronics
The consumer electronics industry relies heavily on rapid prototyping to test new product designs, optimize ergonomics, and enhance user interfaces before launch.
4. Aerospace and Defense
In aerospace, rapid prototypes are essential for creating lightweight components and testing them under extreme conditions. This can significantly enhance safety and fuel efficiency in aircraft designs.
Choosing the Right Plastic Rapid Prototypes Manufacturer
Selecting the best manufacturer for your rapid prototyping needs is essential. Consider the following factors:
1. Expertise and Experience
Evaluate the manufacturer's experience in your industry. A provider with specialized knowledge will understand your requirements better and produce superior prototypes.
2. Technology and Capabilities
Understand the technologies the manufacturer employs. Ruoad and advanced prototyping methods indicate that they can handle a wider range of projects.
3. Quality Assurance Practices
Investigate the quality control measures the manufacturer has in place. A strong quality assurance program is vital for ensuring high-quality prototypes.
4. Customer Support and Communication
Effective communication channels and support can streamline the prototyping process, making it easier to address any concerns and improve collaboration.
Conclusion
In conclusion, the role of plastic rapid prototypes manufacturers is critical in today's manufacturing landscape. Their ability to produce high-quality, functional prototypes quickly and affordably enables businesses to innovate and stay ahead in competitive markets. By understanding how these manufacturers operate and the benefits they offer, businesses can make informed decisions that enhance their product development strategies. Embracing rapid prototyping is a step towards embracing innovation and achieving excellence in product design.